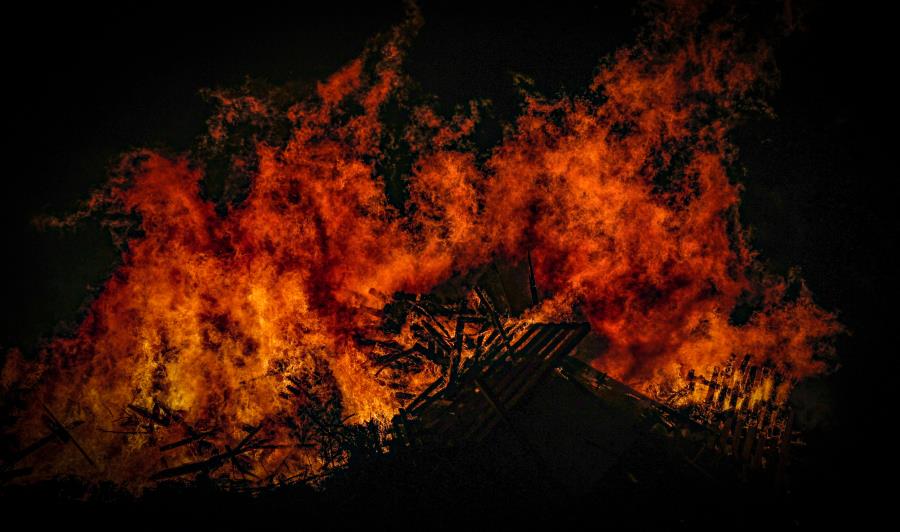
Custom Formulated Flame Retardant Textile Backings
In 1988 the UK implemented the Furniture and Furnishing (Fire Safety) Regulations (FFR’s) following a major fire in the furnishings department of the Woolworths store in central Manchester. Tragically 10 people lost their lives in the fire. The regulations led to the use of flame retardants in the foam and on the back of the textiles used in furniture.
The introduction of this legislation saved lives. In late 2009 The Department for Business, Innovation and Skills (BIS) published a report comparing the number of fires, injuries and deaths attributable to Furniture and Furnishings for the periods 1981-5 and 2002-7. Overall, in the period 2002-07, the analysis suggests that the FFR’s account for 54 fewer deaths per year, 780 fewer non-fatal casualties per year, and 1,065 fewer fires each year.
To meet the requirements of the Furniture and Furnishing (Fire Safety) Regulations (FFR’s) textiles are back coated with water based, polymer bound, flame retardant compounds. For over 20 years Formulated Polymers have manufactured a range of products which enable textile coaters to meet the FFR’s.
The range of furniture for sale in the UK is enormous. Consequently, a huge number of different types of fabrics are needed to meet this demand. These vary massively in both composition and construction. Both natural and synthetic fibres are used. These include cotton, wool, polyester, nylon, polypropylene, acrylics and various combinations of these for example polyester/cotton. Furnishing textiles will vary in massively in construction, unit weigh and thickness. There are woven textiles i.e. plain weave, twill weave and silk weaves; knitted textiles i.e. weft and warp knitted fabrics and nonwoven/fibre bonded fabrics.
Textile back coaters use different coating methods. Coatings may be applied by foaming, through a screen or as a paste. Drying facilities also vary.
Meeting the FFR’s using such a wide range of textiles and application methods necessitates the use of a range of different back coatings. At Formulated Polymers we can tailor our products to your specific needs.
There are many factors which need to be considered when deciding on the composition of a back coating for different textiles and processing methods.
Typically, the active flame retardant components in flame retardant textile back coatings are the halogens bromine and chlorine. Of these bromine is the more effective. These are usually combined with antimony trioxide which acts synergistically with halogens vastly improving their efficiency. Other flame retardant materials may also be incorporated. The amount and ratios of all these components will affect the fire performance of the finished composition.
The total solids content of the compound will affect the amount of material applied to the textile. Compounds with a higher solids content will give higher coating weights. Lower solids will obviously give lower coating weights. In general solids contents between 40 and 60% are most commonly used. Solids content will also affect drying times. The higher the solids content the quicker the compound will dry.
Compound viscosity will affect pickup weights and the degree to which the compound penetrates the fabric. Lower viscosity grades will tend to penetrate further into the fabric. Higher viscosity grades will tend to remain on the back of the textile.
For compounds applied by foaming both the foam density and foam viscosity will affect the amount of pickup. Lower foam densities result in lower application weights. Foam viscosity will also affect the degree of penetration into the textile.
At Formulated Polymers we make a range of flame retardant back coatings which enable end users to meet the requirements of the FFR’s. If we don’t have a product on our range to meet your requirements, then we can tailor one to your specific needs.